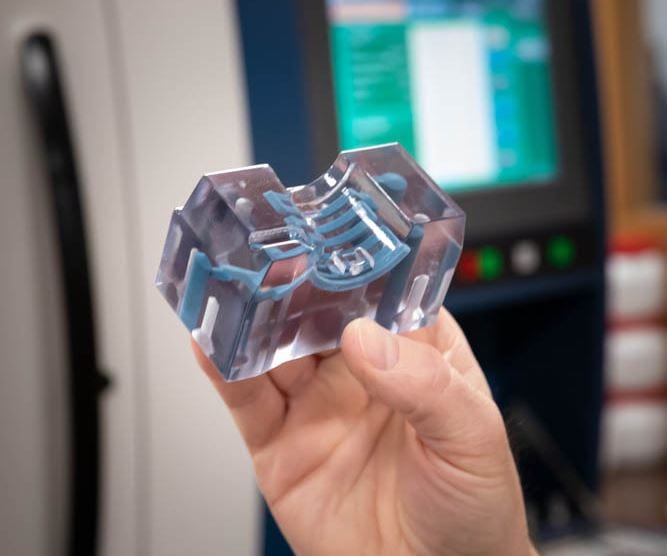
St. Paul, MN (December 5, 2019) — Owen Greenings & Mumford Ltd (OGM) engineers the highest quality technical plastic injection moldings and assemblies, using advanced injection molding, automation and additive manufacturing technologies.
The company’s plastic injection molding knowledge and skills help customers throughout the industry reduce lead times and time to market, while enhancing the quality, functionality and performance of injection molded parts.
OGM’s investment in the Matsuura LUMEX Avance-25 metal additive and machining technology, combined with their continually developing expertise in this emerging field, results in an innovative solution for producing plastic injection mold tooling.
Using the latest 3D metal additive printing technology, the Matsuura LUMEX, OGM builds true conformal cooled inserts for injection mold tools.
OGM explains traditional methods using machining, cross-drilling and EDM can only produce straight cooling paths. This limits the efficiency of cooling within each injection mold tool, leading to problems with distortion and the quality of each injection molded part.
The company’s solution creates conformal cooled mold tool inserts:
- With complex curved, shaped or spiral cooling channels
- Easily formed in small, narrow or awkwardly shaped inserts
- Cooling channels that precisely follow the shape of each injection mold tool insert
The result is a new generation of injection mold tools:
- Consistent and accurate cooling characteristics across the entire forming area
- Exceptionally high consistent quality injection molded plastic parts.
What is conformal cooling?
Conformal cooling is the production of cooling channels within plastic injection mold tools that follow the shape of the cavity and core. This ensures that every critical part of the mold tool is cooled in a controlled and consistent manner. The results include better part quality and faster cycle time.
Until recently, it has been difficult to engineer effective conformal cooled injection mold tools, as channels need to be drilled directly into each mold tool; running straight cooling channels close enough to the mold cavity for efficient heat transfer can be challenging, especially when parts have complex geometries. Cooling channels also must compete for space with other features, such as ejector pins or moving inserts, further reducing the efficiency of the cooling process.
Although injection mold toolmakers have developed solutions to this problem they add to the time, complexity and cost of producing each injection mold tool or mold tool insert.
OGM was founded in 1962 in a workshop in Oxford with a single injection molding machine.
Over the next 40 years, Bev Wightman developed the business successfully with growth based on outstanding customer service, continuous innovation, the highest quality and a commitment to long term partnerships that add real value to every customer.
In 2001, Paul Wightman took over the business from his father and as Managing Director has continued to uphold the same core values.
More recently, ongoing success has led to the creation of a diversified group of companies within the OGM Holdings Group. Manufacturing from four factories in the UK, OGM now operates in Oxford and South Wales, and owns businesses in Bedford and Derby producing catering consumable products and printed films for packaging.
Hybrid Metal Additive Manufacturing and machining is an extremely effective method of creating conformal cooled injection mold tool inserts.
Efficient injection mold cooling is essential to achieving short cycle times and high-quality parts. However, creating the more effective conformal style of cooling channels, particularly within complex shaped molds, can be challenging.
Speed is of the essence in the production of injection molded components. Manufacturers need to get their designs from concept to production as quickly as possible so that time-to-market targets can be met. Molders also need to achieve the shortest possible part production cycle times to maximize productivity and keep unit costs down.
The manufacture of mold tools suitable for the high-volume production of complex parts is a time-consuming process; lead-times of up to four months between design sign-off and first part production are not uncommon. Moreover, the performance of a tool – especially its ability to cool parts effectively prior to ejection – determines the cycle time, quality and overall productivity of the molding process.
Water plays a critical role in the plastic injection molding process, ensuring that the part is cooled and solidified in the mold cavity and gains sufficient structural rigidity prior to it being ejected. To achieve the short cycle times and high productivity rates required for low cost, high volume parts, cooling water is passed through channels created within the mold tool to accelerate this solidification process.
As well as boosting injection molding productivity, rapid, even cooling is also vital for part quality. Appropriate control of the cooling rate affects the mechanical properties and surface finish of the part, and if areas of the material are insufficiently cooled within the mold, they can shrink excessively after ejection, leading to distortion, poor tolerances and unacceptably high reject rates.
Conventionally, these cooling channels are drilled through the mold material during tool manufacture; and while this approach is simple, where the part geometries are more complex, it can be difficult to run straight cooling channels close enough to the mold cavity for efficient heat transfer.
A further complication arises when cooling channels have to compete with features such as ejector pins, or moving inserts, for space within the tool. Illustrative of this is the production of box shapes, such as electronic enclosures, where the best position for the ejectors is usually at the more structurally strong corners. Unfortunately, these points are also the hardest to cool and even minor shrinkage at the corners of a box due to inadequate cooling can lead to significant distortion of adjacent walls.
Sometimes, as in the case of the slender cores used to create the internal surfaces of thin hollow parts, it is impossible to provide a straight cooling path through the tool and often requires elaborate workarounds during tool manufacture. For example, a toolmaker might drill two parallel channels, connect them with a cross channel and then add material to seal its ends, or they may insert a baffle into a larger blind hole to create inlet and outlet pathways for coolant. These all add cost and complexity to the mold making process, while some mold features may be too small to accommodate them altogether.
Poor cooling performance creates a dilemma for plastic injection molders. Either they accept high levels of distortion, or they slow down the production process, allowing the part to cool in the mold for longer. Taking the latter route inevitably increases the overall cycle time, damaging productivity and driving up part costs.
Conformal cooling
Changing the shape of the fluid channels within the mold from straight lines to curves allows them to follow the part surfaces more closely, negotiate obstacles like ejector pins, and squeeze into inaccessible areas. This ‘conformal cooling’ approach has been around for a long time, but it is rarely used in production applications, as there is significant manufacturing complexity involved in building tools with such conformal cooling channels.
Using conventional subtractive machining, conformally cooled tools require molds to be created in laminations. The cooling channels are machined into the surface of these laminations, which are then stacked on top of each other to create the finished tool. The technique adds significant time and cost to the toolmaking process; it can also result in less durable tools and does not provide a solution for all part geometries.
More recently, additive manufacturing technologies have provided an alternative method of incorporating conformal cooling channels in plastic injection molds. Direct metal laser sintering, for example, allows the formation of complex shapes from powder metallic materials, enabling channels of almost any shape to be incorporated into a design; the process does have its drawbacks, however. It is costly and time consuming, for one, and the surfaces created are not smooth enough for the purposes of injection molding, requiring extensive secondary machining operations and adding further to costs and tool production lead times.
A new, fast hybrid approach
There is now a new technique which promises to overcome some of the barriers that have prevented the wider uptake of conformal cooling by the industry. Combining additive manufacturing and conventional CNC machining technologies, the Matsuura LUMEx Avance-25 now installed at OGM’s site near Oxford – and believed to be the first of its kind in the UK – builds steel mold tools complete with conformal cooling channels layer by layer using a laser.
As each layer is deposited, an automated secondary CNC machining process removes excess material to provide a dimensionally accurate, fine surface finish. The material produced by this process is hard enough (HRC 35) to meet the needs of many production applications without subsequent heat treatment; if required, a full range of textured or polished surface finishes can be applied using industry standard secondary processes.
Cooling channel designs are able to make optimal use of the capabilities offered by this process, to create parts dubbed ‘Conformal Cool Inserts’ by OGM. For example, as well as allowing cooling channels to take any route through the tool, the process also removes the necessity for those channels to be round. Elliptical, rectangular and even teardrop designs can maximize heat transfer for a variety of applications. Moreover, special ‘trip’ features can be incorporated within the channels to promote turbulent coolant flow which increases the heat transfer rate.
OGM says that its new approach allows customers to obtain steel tools suitable for high volume production in as little as four weeks, less than a third of the time required for conventional toolmaking. Furthermore, the technology developed to manufacture complex conformal cooling channels – which can significantly improve the in-mold cooling of complex parts – not only boosts part quality but can also cut molding cycle times by up to 20%.
OGM is currently taking this development forward with a variety of offerings, including custom-built inserts that can be incorporated into conventionally manufactured tools to address hard-to-cool areas, as well as a range of standard inserts, including ejector units with built-in cooling channels.
The ability to build complete mold tools – complete with complex cooling channel geometries and designs – in a one-hit automated process can lead to significant design-to-part lead-time reductions. Thanks to hybrid additive manufacturing, compelling commercial benefits are offered to companies operating in fast-moving, time-sensitive markets.
Portions of this article are derived from Production Engineering Solutions (https://www.pesmedia.com/) and OGM’s website.
To discover more about OGM, please visit: www.ogm.uk.com
Matsuura Machinery USA, Inc., located in St. Paul, MN is the U.S. subsidiary of Matsuura Machinery Corporation in Japan. Since 1935, Matsuura has been the forerunner in designing innovative technology and manufacturing solutions to a variety of industries around the globe. Matsuura Machinery USA, Inc. delivers unmatched excellence in 5-axis, vertical, horizontal, linear motor, multi-tasking CNC machine tools and machines with a powder bed metal AM platform with machining capability. Matsuura Machinery USA, Inc. provides the service, applications and technical field support that have always been the Matsuura standard for business.
For more information on Matsuura LUMEX products, please contact: [email protected] or visit: www.matsuurausa.com.