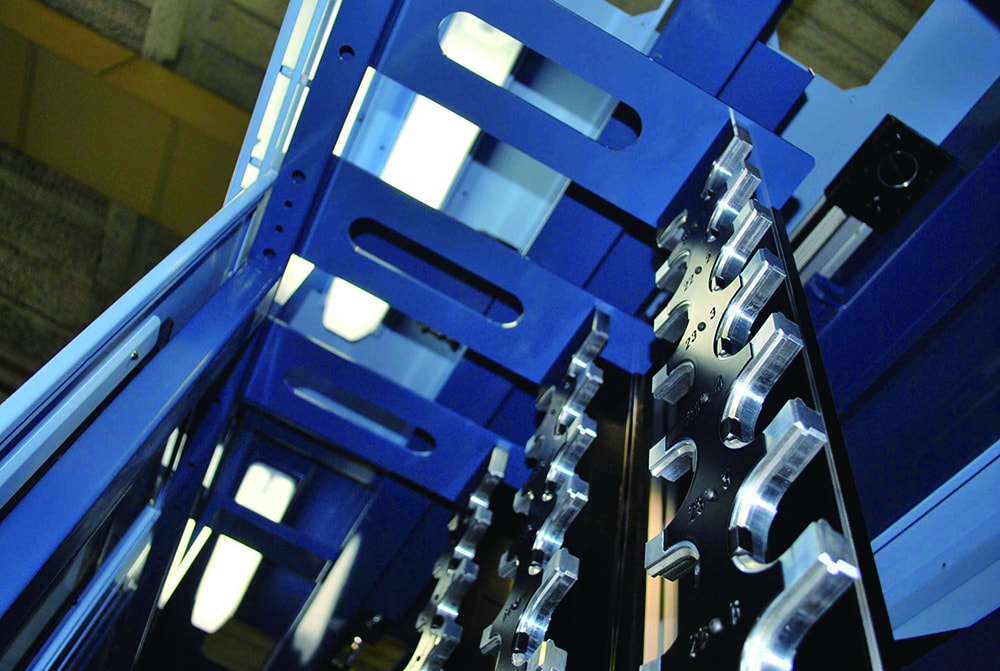
St. Paul, MN (October 15, 2019) — Matsuura’s original automation and unmanned running systems provide solutions for organizations facing labor shortages by utilizing working hours effectively. With the deficiency in skilled labor to operate CNC Machines, automation provides the potential for expanding production and increasing profit while decreasing employment costs.
Matsuura’s systems can be installed as an option for Matsuura’s 3-axis/5-axis machining centers to automate tool changes and pallet changes using programs, drastically improving the productivity.
“People usually think of automation in high volume production environments, typically with 6-axis robots, but automating the small lot size production is different and more challenging,” St. John said.
Installing ATC tool magazines and APC pallet systems as options with Matsuura 5-axis machining centers allows the machines to automatically continue production without human intervention, even during the night.
Few machine tool builders have perfected this type of automation and the shops incorporating the technology have tremendous competitive advantages. Matsuura’s line of MAM72 models fit this application perfectly. MAM stands for Matsuura Automated Manufacturing and 72 is the hours in a weekend. The machines are built from the ground up to run unattended.
Another way to effectively achieve automation is to combine operations. Machining 5 sides of a part along with angled holes and surfaces is essentially automation compared with flip flopping the same part through six or more separate operations.
This approach to reducing set-up time, reducing labor content and combining of operations does not need to be expensive, nor time intensive to implement. 5-axis machines today are simpler, less expensive, and easier to program than in years past.
“You may never do simultaneous 5-axis contours, but you are going to machine all sides of that billet. Why not do 5 sides in one set-up – that’s the key to improved part accuracy, lower fixturing costs, and reduced labor costs today,” St. John explained.
Investing in this level of automation allows shops to stay globally competitive.
Combining operations using 5-axis machining centers and running unmanned using pallet systems is equally effective in the medical component applications or any complex parts requiring close tolerances.
Matsuura’s customers often run the high-mix, low-volume components which require more engineering and set-up during the business day. Then, they change over to the unmanned production, where the pallets in the system run all night.
“Many companies claim that you can run three shifts, but with Matsuura you really can,” St. John concluded.
Matsuura Machinery USA, Inc., located in St. Paul, MN is the U.S. subsidiary of Matsuura Machinery Corporation in Japan. Since 1935, Matsuura has been the forerunner in designing innovative technology and manufacturing solutions to a variety of industries around the globe. Matsuura Machinery USA, Inc. delivers unmatched excellence in 5-axis, vertical, horizontal, linear motor, multi-tasking CNC machine tools and machines with a powder bed metal AM platform with machining capability. Matsuura Machinery USA, Inc. provides the service, applications and technical field support that have always been the Matsuura standard for business.
For more information about Matsuura, please contact: [email protected] or visit: www.matsuurausa.com.