St. Paul, MN (May 14, 2020) —From Yasuo Matsunaka, Redshift by AUTODESK:
Injection molding is essential to mass-producing plastic parts with complex shapes. To create higher-quality products at lower costs, the priority has been to develop advanced cooling systems for melted materials. But that is difficult, time-consuming work, even for skilled engineers. Could automating the design of mold-cooling water channels help the engineers working on this challenge?
In Japan, Panasonic Corporation’s Life Solutions Company is betting on just that—and has developed a new manufacturing method for mold-cooling water channels by using the LUMEX Avance-25, the world’s first hybrid metal 3D printer. Combining additive manufacturing and milling, the result is a conformal-cooling system (which lays out the cooling channels conforming to the shape of the products) that has reduced cooling times by 20% compared to conventional methods, where channels are drilled straight through the mold.
Seiichi Uemoto is an analyst at the company’s Manufacturing Engineering Center, where the molds are designed and fabricated. He holds classes on mold design and supports computer-aided engineering (CAE) skill development to impart the advanced techniques needed for designing molds.
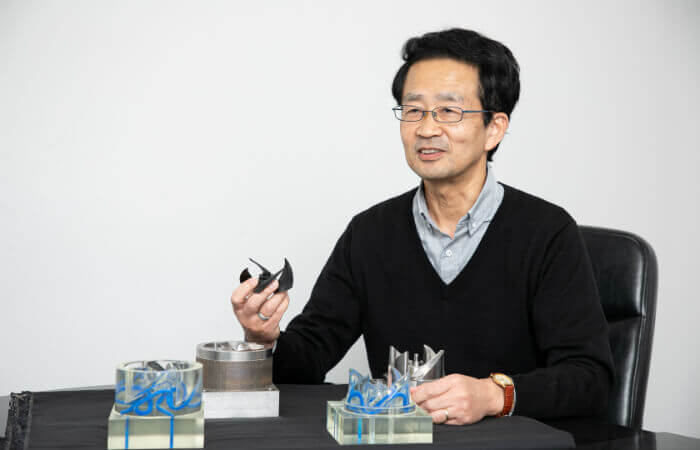
Seiichi Uemoto, of Panasonic’s Life Solutions Company Manufacturing Engineering Center, was inspired to try automating metal mold designs.
While he was optimizing the design of cooling loops for box-shaped metal molds (presented at the 2014 InterMold exhibition), Uemoto used warping data from molded products to analyze gap spaces between cooling channels. This work inspired him to try automating the metal mold designs.
“I thought that with the right settings in place, I could use generative design to automatically create mold-cooling channels,” Uemoto says. He saw how generative design applies structural analysis, efficiently realizing shapes with reduced weights.
“Topology optimization can produce only one solution from the conditions provided to the system,” Uemoto says. “It is difficult to produce something with smooth contours from the generated result. But it became apparent to me that generative design would inherently result in smoother shapes. I felt with generative design, we would be able to effectively generate multiple concepts that took manufacturing principles into account.”
A Workflow Supported by Generative Design
Uemoto hoped that applying generative design to molds would result in new mold shapes and automate the design process itself. The company’s highly skilled designers are developing a variety of products supported by Autodesk Moldflow, which performs molding simulations to further refine their designs. “I felt that if we use automatic design to provide insights designers may not come up with by themselves, it would give them more freedom in their work,” Uemoto says.
To achieve this, Panasonic collaborated with the Autodesk Advanced Consulting team working out of Birmingham, England, on a project that applied generative design to mold-cooling water channels. They chose the fan blades used in duct-ventilation systems, which were already being mass-produced, as their test object.

The blade mold used in the pipe fan (far left) was selected as the target for generative design. Courtesy of Life Solutions Company, Panasonic Corporation.
These fan blades were small with a complex shape. An expert designer provided constraints for the fan blade’s initial shape, a range of conditions for the water channels to be generated, and restrictions to prevent the channel paths from influencing the fine details of the molded product.
During the generative-design process, the shape of the product changed over numerous iterations until only the essential components remained for creating the required water channels. Because Panasonic’s engineers had already designed highly refined molds, Uemoto thought it might be difficult for the software to drastically improve upon the original design’s efficiency. “But I was really impressed by the fully formed models that were being automatically generated,” he says.
Even more surprising was the layout of the water channels. Some of the design includes the channels that were set to run along the outer shell of the mold, suddenly branched out in unique ways. Uemoto describes the resulting design as something he had never even imagined. “The shapes provided by the generative-design process could never have been conceived by any one person,” he says.
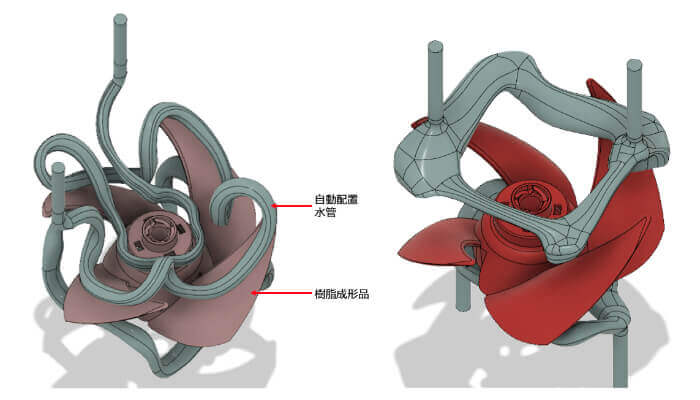
Case C (left) was generatively designed with its shape constrained to a designer’s initial shape; Case D (right) was generatively designed with its shape constrained only by the initial shape of the outer shell. Courtesy of Life Solutions Company, Panasonic Corporation.
Proving Capability Through Production
Following the design process, four different mold samples were manufactured: Case B, the original part already used in manufacturing, designed by a veteran engineer; Case C, an automated, generative design based on the original part; Case D, a generative design with looser restrictions on its shape; and Case E, the same Case C design but with additional water channels. Products made using the molds were precisely measured to assess each mold’s performance.
The molded products’ measurements showed there was very little difference in performance between a mold using automatically generated cooling channels compared to the veteran engineer’s design. “I could see how the design was calculated to shape the product through shifts in temperature within the mold,” Uemoto says. “It was quite remarkable. Ultimately, we obtained smoothly contoured CAM [computer-aided manufacturing] data, fulfilling our goal of working with automated design.”
It takes an experienced engineer around eight hours to design a mold, and there is currently no way to streamline that process, regardless of skill level. Despite this, Uemoto expects that this project’s success will lead to solutions that will reduce the design burdens placed on these engineers.
“This is a great development,” Uemoto says. “If this becomes a part of a packaged software in the near future, it could lead to a solution for speeding up tasks and allow us to develop programs focusing more on temperature control. That should benefit a wide range of users and applications.”
More from AUTODESK: HERE.
With Matsuura’s LUMEX technology, Deep Ribs & Conformal Cooling Channels significantly reduce product cycle time.
Matsuura customers are seeing the value that comes with implementing additive manufacturing technology into their tools. These include conformal cooling channels, porous venting, and virtually no concerns over deep ribs. Secondly, it’s quick-turn manufacturing, which means the ability to build a production tool in days versus weeks or months, with reduced tooling costs. Finally, those toolmakers who are also injection molders are reaping the additional benefits of cycle time savings, thanks to an additively manufactured mold’s far greater cooling capabilities.
Matsuura has multiple customer case studies, all showing 25% to 45% reductions in cycle time reductions, the Matsuura LUMEX Technology is transformative in the industry.
Matsuura’s LUMEX Technology relies on one-machine, one-process manufacturing of complex molds and parts by fusing metal laser sintering technology with high speed milling technology. The Hybrid technology creates a “finished” part with machined surface finish and accuracy, without inducing the additional variation caused by multiple machine set-ups and part handling.
The Matsuura LUMEX produces highly accurate parts from metal powders that are melted and sintered using a laser while surfaces are precisely milled at high speeds. This technology allows the ability to “grow” a metal component in layers with complex internal features and fine mill those internal features, as the layers are added, to give a perfect surface finish are what makes the LUMEX Series such a distinctive, unique and remarkable production platform and machine tool.
Matsuura Machinery USA, Inc., located in St. Paul, MN is the U.S. subsidiary of Matsuura Machinery Corporation in Japan. Since 1935, Matsuura has been the forerunner in designing innovative technology and manufacturing solutions to a variety of industries around the globe. Matsuura Machinery USA, Inc. delivers unmatched excellence in 5-axis, vertical, horizontal, linear motor, multi-tasking CNC machine tools and machines with a powder bed metal AM platform with machining capability. Matsuura Machinery USA, Inc. provides the service, applications and technical field support that have always been the Matsuura standard for business.